As someone who’s been watching CNC technology closely over the years, I’m genuinely excited about where things are headed in 2025.
CNC (Computer Numerical Control) technology has already reshaped manufacturing, but honestly, I believe we haven’t seen anything yet.
With advances happening at lightning speed, we’re looking at a future that feels straight out of science fiction—except it’s real and happening now.
Automation Goes Next-Level
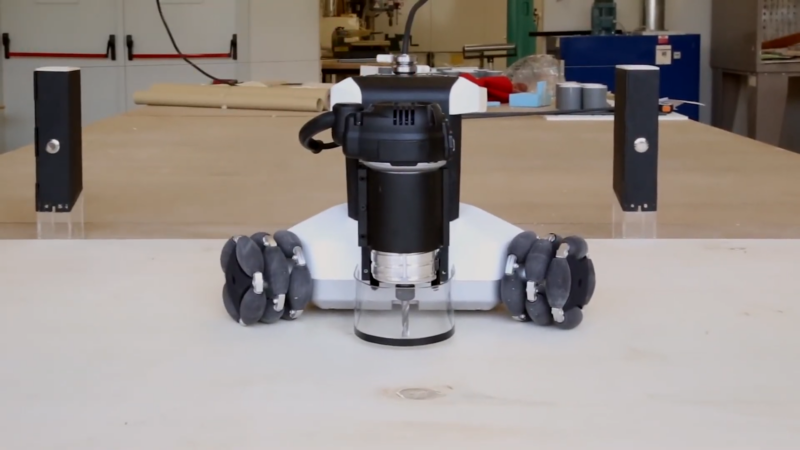
Automation isn’t a new concept, especially in CNC machining, but the automation we’re seeing now is next-level stuff.
Imagine machines that don’t just execute programmed instructions but can also make real-time decisions, correcting errors before they happen. We’re talking about smarter, safer, and far more efficient manufacturing.
Robots Becoming Teammates
Remember when robots were just big, bulky machines that required safety barriers?
Fast forward to today, and robots have evolved into cooperative teammates, working seamlessly alongside human operators. By 2025, collaborative robots—or cobots—will become common sights in CNC shops.
Here’s what makes cobots special:
When I first saw a cobot in action, I was amazed by how gentle yet precise its movements were—almost human-like in their care.
Autonomous CNC Machines
Another development I’m genuinely intrigued by is autonomous CNC machinery. Imagine your CNC machine detecting and adjusting for wear on a tool automatically, reducing downtime and preventing costly mistakes.
With advanced sensors and software, autonomous machines monitor every aspect of the machining process, ensuring consistent precision.
I know some folks worry about losing control, but consider it like having a reliable assistant who keeps an eye on the details so you can focus on strategic planning.
Artificial Intelligence: A Game-Changer in CNC Machining
AI has already shaken up industries from healthcare to finance, but I think its real potential in CNC machining is still unfolding.
AI-powered CNC machines are not just fancy gadgets; they’re shaping the very future of manufacturing by increasing efficiency, precision, and even creativity.
Smart Predictive Maintenance
Imagine having a machine that can tell you exactly when it needs servicing—long before a breakdown happens. That’s exactly what AI-powered predictive maintenance does.
By analyzing historical data and real-time conditions, the CNC system flags potential issues early, cutting downtime significantly.
From a business standpoint, predictive maintenance saves money. From a human perspective, it reduces stress. Nobody enjoys unexpected breakdowns—trust me, I’ve been there, and it’s not fun.
Intelligent Adaptive Control
Another AI-driven innovation I’m excited about is adaptive control. Simply put, it lets CNC machines adjust operations on the fly.
For instance, if the material being machined suddenly behaves differently, the system recognizes and compensates automatically, ensuring consistent quality without human intervention.
Adaptive control doesn’t just make machining more accurate; it boosts confidence. Do you know the feeling when you hit ‘start’ and hold your breath, hoping nothing goes wrong?
Well, adaptive control gives you peace of mind because you know your machine can handle surprises.
Sustainability Becomes a Priority, Not an Option
View this post on Instagram
I care deeply about sustainability, and thankfully, the manufacturing industry is finally catching up. In 2025, sustainability in CNC machining isn’t just a nice-to-have—it’s becoming a core requirement. Here’s how:
Eco-Friendly Materials and Processes
Manufacturers are embracing eco-friendly materials, reducing waste, and minimizing energy usage. Biodegradable cutting fluids, recyclable materials, and energy-efficient machinery are becoming standard practice.
It’s encouraging to see businesses genuinely committed to protecting the environment.
Think about it—if we can reduce environmental harm while improving our bottom line, why wouldn’t we?
Energy-Efficient CNC Equipment
Energy efficiency will become crucial, not only for environmental reasons but also because it directly impacts cost. CNC machines equipped with energy-saving features, like adaptive speed control and automatic shutdown when idle, will dominate the market.
I’ve seen energy-efficient CNC equipment firsthand, and the difference it makes is significant—not just on energy bills, but also in reducing a facility’s carbon footprint.
As someone who values both efficiency and sustainability, this trend is a clear win-win.
3D Printing and CNC Machining Join Forces
@engler3d This is hobby CNC machining done by me, with lot of 3D printed holders and even more creative problem solving.✌🏼⚙️#engler3d #techtok #tech #student #cnc #programming #tip #diy #machining #3d #3dprinted #dream ♬ original sound – MJ Show and Tell
3D printing and CNC machining have often been viewed as separate, even competing technologies.
But lately, I’ve noticed they’re increasingly used together, complementing each other in fascinating ways. By 2025, I believe their integration will become mainstream, revolutionizing manufacturing processes.
Hybrid Machines—The Best of Both Worlds
Hybrid CNC machines, which combine subtractive CNC machining and additive manufacturing (3D printing), are gaining traction.
With hybrid machines, complex parts that once required multiple processes and machines can be produced efficiently in a single setup.
Here’s why hybrid machines excite me:
When I first saw hybrid technology in action, I was blown away by how quickly it transformed raw materials into intricate, fully finished products.
Prototyping to Production: Seamless Transition
Combining CNC and additive technologies means going from prototype to full-scale production seamlessly. Companies can iterate designs faster, make real-time adjustments, and move quickly to mass production without switching equipment or suppliers.
From my experience, this seamless transition isn’t just efficient—it’s liberating. It encourages innovation, creativity, and risk-taking because it’s easy to make adjustments at any point in the process.
The Human Factor: Workers and CNC Technology in Harmony
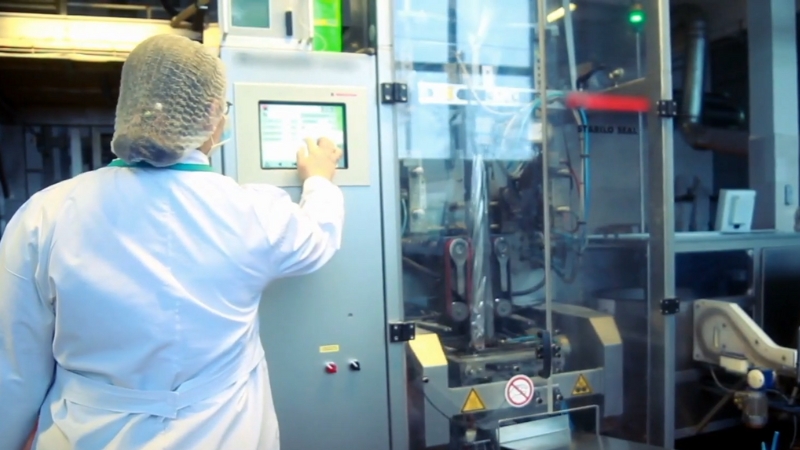
We can’t talk about the future of CNC without considering how it affects people. I’ve heard concerns that advanced technology might push humans out of the equation.
But in reality, the role of skilled workers in CNC environments is evolving—not disappearing.
Upskilling Becomes Essential
As CNC machines get smarter, the role of workers shifts from manual tasks toward oversight, programming, and problem-solving. Workers who can operate, maintain, and program advanced CNC equipment will become incredibly valuable.
I believe investing in training and upskilling workers is crucial.
Enhanced Workplace Safety
One major benefit of advanced CNC technology is safety. AI-powered systems and automated monitoring drastically reduce workplace accidents. As someone who has seen accidents happen due to fatigue or human error, I can’t emphasize enough how important improved safety is.
By 2025, CNC workplaces will likely become safer, less stressful, and more worker-friendly environments. And that’s something worth celebrating.
Connectivity and Industry 4.0 Integration
Industry 4.0 is revolutionizing machining! ⚙️
Discover how this transformative era is shaping the future of manufacturing in our latest article.https://t.co/hmC2XztSpl
#Industry4.0 #Machining #Manufacturing #Technology #CNC pic.twitter.com/LitHCJlqFh
— MachiningCloud (@machiningcloud) February 6, 2025
Industry 4.0—also known as the Industrial Internet of Things (IIoT)—is more than just a buzzword; it’s reshaping CNC technology fundamentally. By integrating CNC machines into connected networks, manufacturers unlock unprecedented efficiency.
Real-Time Data and Transparency
Connected CNC machines provide manufacturers with real-time data, enabling better decision-making. Imagine knowing exactly how every machine in your facility performs at any given moment, adjusting workflows instantly to optimize productivity.
Here are some of the benefits:
I’ve personally experienced the benefits of real-time connectivity—it truly transforms the way you work, making you feel informed and empowered rather than overwhelmed.
Cloud-Based CNC Operations
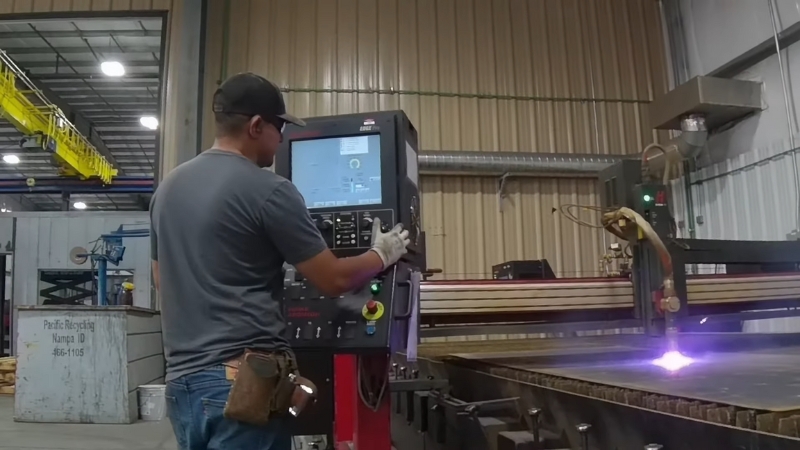
Cloud integration takes CNC connectivity even further. Cloud-based CNC platforms allow secure data storage, remote access, and seamless collaboration between teams and machines, regardless of physical location.
Cloud-based operations aren’t just convenient—they represent a fundamental shift in how manufacturing is done. You can manage your CNC processes from home, during travel, or anywhere with an internet connection.
Final Thoughts
Looking ahead to 2025, I’m genuinely optimistic about where CNC technology is headed. Automation, AI integration, sustainability, hybrid machinery, and connectivity are not distant dreams—they’re our reality today.
CNC technology isn’t just becoming more advanced; it’s becoming smarter, safer, and more accessible for businesses of all sizes.
Yet, what excites me most is how human-centric the future of CNC remains. Despite all technological advancements, it’s people who ultimately drive innovation, make crucial decisions and shape manufacturing’s future.